Mission M
Vollautomation
Industrialization of Core Printing (ICP)
Pioniere der Industrialisierung des Kerndrucks und der additiven Serienfertigung
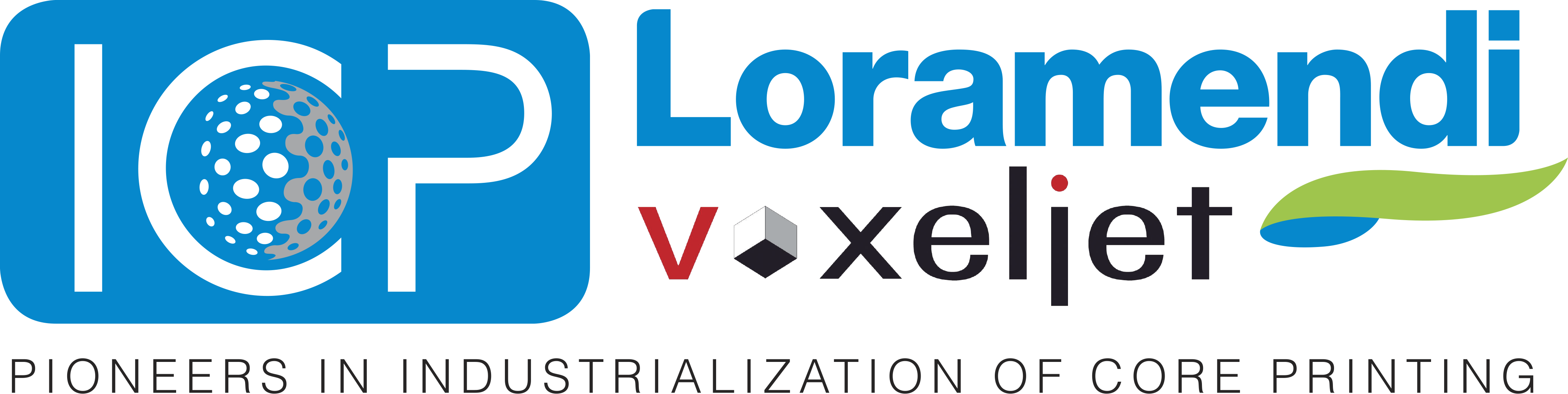
Im Rahmen des Kooperationsprojektes Industrialization of Core Printing (ICP) haben wir gemeinsam mit Loramendi, einem spanischen Experten für Gießereiequipment, die weltweit erste vollautomatisierte additive Fertigungszelle installiert und in Betrieb genommen.
Installiert ist die Zelle in der Leichtmetallgießerei der BMW Group Plant in Landshut, Deutschland, und produziert pro Monat mehrere Tausend Wassermantelkerne für die Zylinderkopfkühlung der B48 Motoren von BMW. Es ist die erste additive Serienfertigungslösung ihrer Art und ein Leuchtturm für alle folgenden Projekte. Besonders stolz sind wir auf unsere VX1300X – eines unserer leistungsstärksten Drucksysteme.
Geringere Investition
Dank schichtbasiertem 3D-Druck entfällt die Notwendigkeit für Werkzeuge gänzlich. Keine langen Lieferzeiten, keine hohen Kosten. Vollautomation begrenzt menschliches Eingreifen auf ein Minimum.
Flexible „Werkzeugwechsel“
Der Wegfall von Werkzeugen bedeutet zeitgleich, dass ohne Rüstzeit ein neue Kerngeometrie auf Knopfdruck additiv gefertigt werden kann. Bspw. Heute ein 4-Zylinder Wassermantelkern, morgen 6-Zylinder.
Geometrische Freiheit
Neue, optimierte und hochkomplexe Designs lassen sich problemlos additiv fertigen. Hinterschnitte sind vernachlässigbar und helfen totgeglaubte Produkte wiederzubeleben und Lebenszyklen zu verlängern.
Seit mehr als 50 Jahren entwickelt Loramendi Anlagen für die Gießereiindustrie und erfreut sich heute eines weltweiten Prestiges. Wir freuen uns sehr über diesen neuen Weg, der die Landschaft der Gießereiindustrie vollständig verändern und neue Standards für die Kernherstellung setzen wird.
Joseba Goitia, General ManagerLoramendi
Anlagen für die Gießereiindustrie
Das Beispiel des ICP-Projekts zeigt, dass durch die Kombination modernster 3D-Drucker mit ausgeklügelter Automatisierungstechnik und geeigneten Nachbearbeitungsprozessen flexible Fertigungszellen geschaffen werden können, die Hunderttausende komplexer Sandkerne pro Jahr mit einem hohen Automatisierungsgrad herstellen können. Mit zunehmender Komplexität der Bauteile kann dies auch als wirtschaftliche Alternative zu Standardproduktionsverfahren wie dem Kernschießen gesehen werden, beziehungsweise entstehen neue Designs, die nur über den 3D-Druck produzierbar sind.
Das ICP-Projekt im Überblick
Die Anforderungen für das ICP-Projekt kamen vom Kunden BMW Group Plant Landshut. Dabei ging es um die Herstellung eines Wassermantelkernes welcher, nach dem Abguss, die Kühlkanäle am Zylinderkopf im Motorblock abbildet.
Die Konstruktion des Kernes ist derart komplex, dass sie die Kerne, auf Grund ihrer Hinterschnittigkeit, ausschließlich additiv fertigen lassen. Durch das komplexe Design kann die Effizienz des Motors um bis zu 30% gesteigert werden, da die Kühlung näher an die Brennkammer gelegt werden kann und so der Wärmeübergang optimiert wird. Die im Automobilbereich üblichen, hohen Stückzahlen sowie die Taktzeit der Anlage waren dabei die größten Herausforderungen
Loramendi und voxeljet haben sich dieser Herausforderung gestellt und mit ICP (Industrialization of Core Printing) erstmals eine flexible Produktionszelle auf Basis von bedrucktem Sand vorgestellt, die mehrere hunderttausend Kerne pro Jahr automatisiert herstellt. Zudem werden im ICP-Projekt ausschließlich anorganische Bindemittel verwendet, was sich positiv auf die Umwelt- und Arbeitsbedingungen auswirkt.
Whitepaper
Erfahren Sie alles über den Status der additiven Serienfertigung und lernen Sie Anwendungsbeispiele kennen.
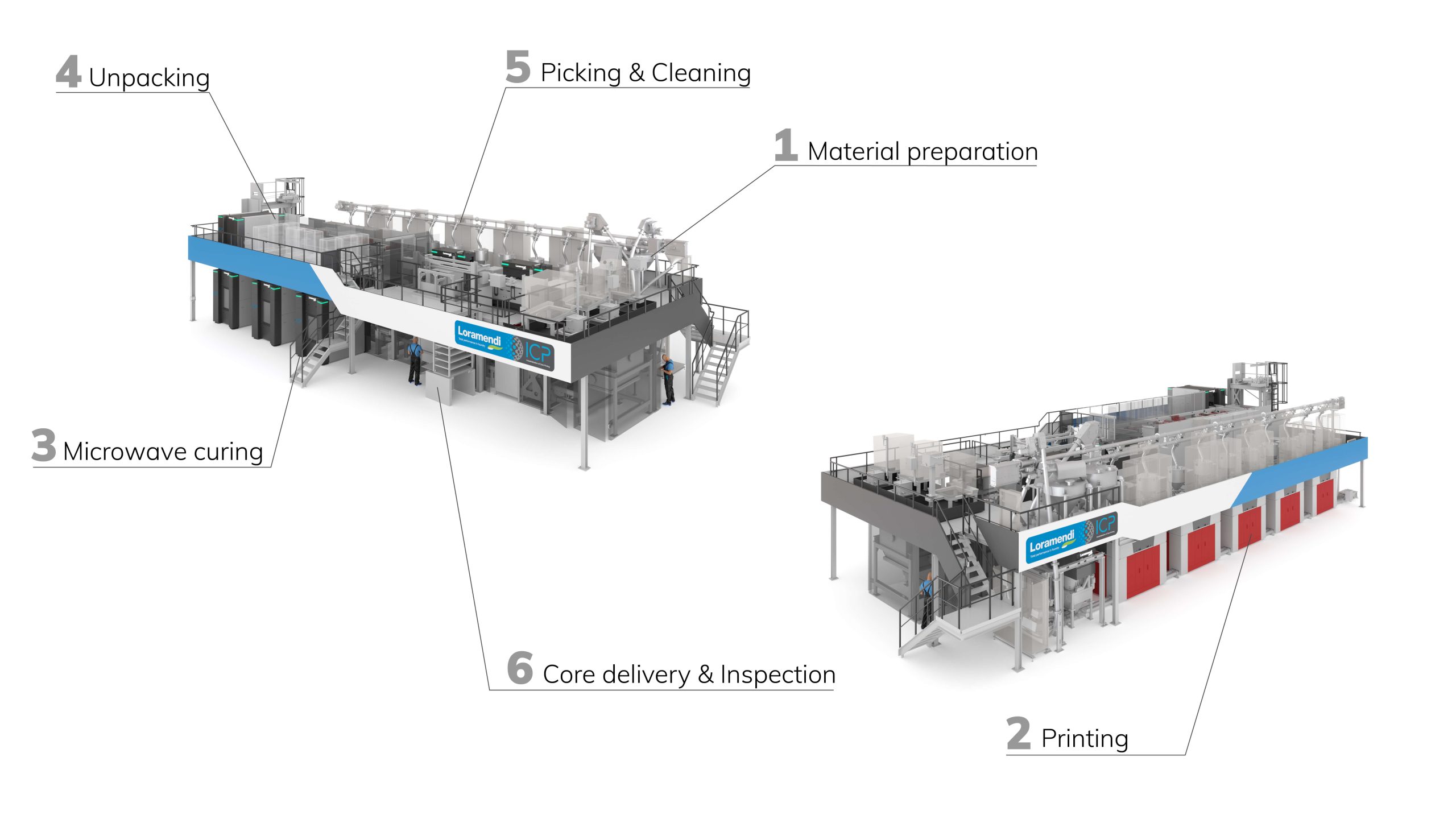
Das vollständige ICP Layout
- Material preparation
- Printing
- Microwave curing
- Unpacking
- Picking & Cleaning
- Core delivery & Inspection
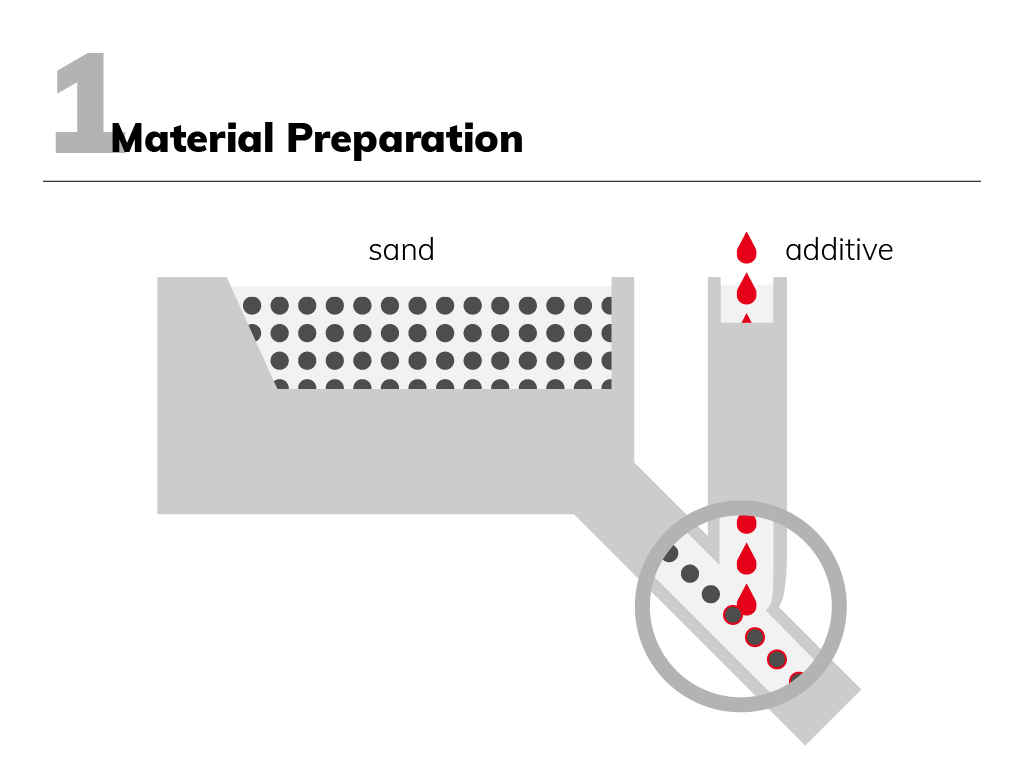
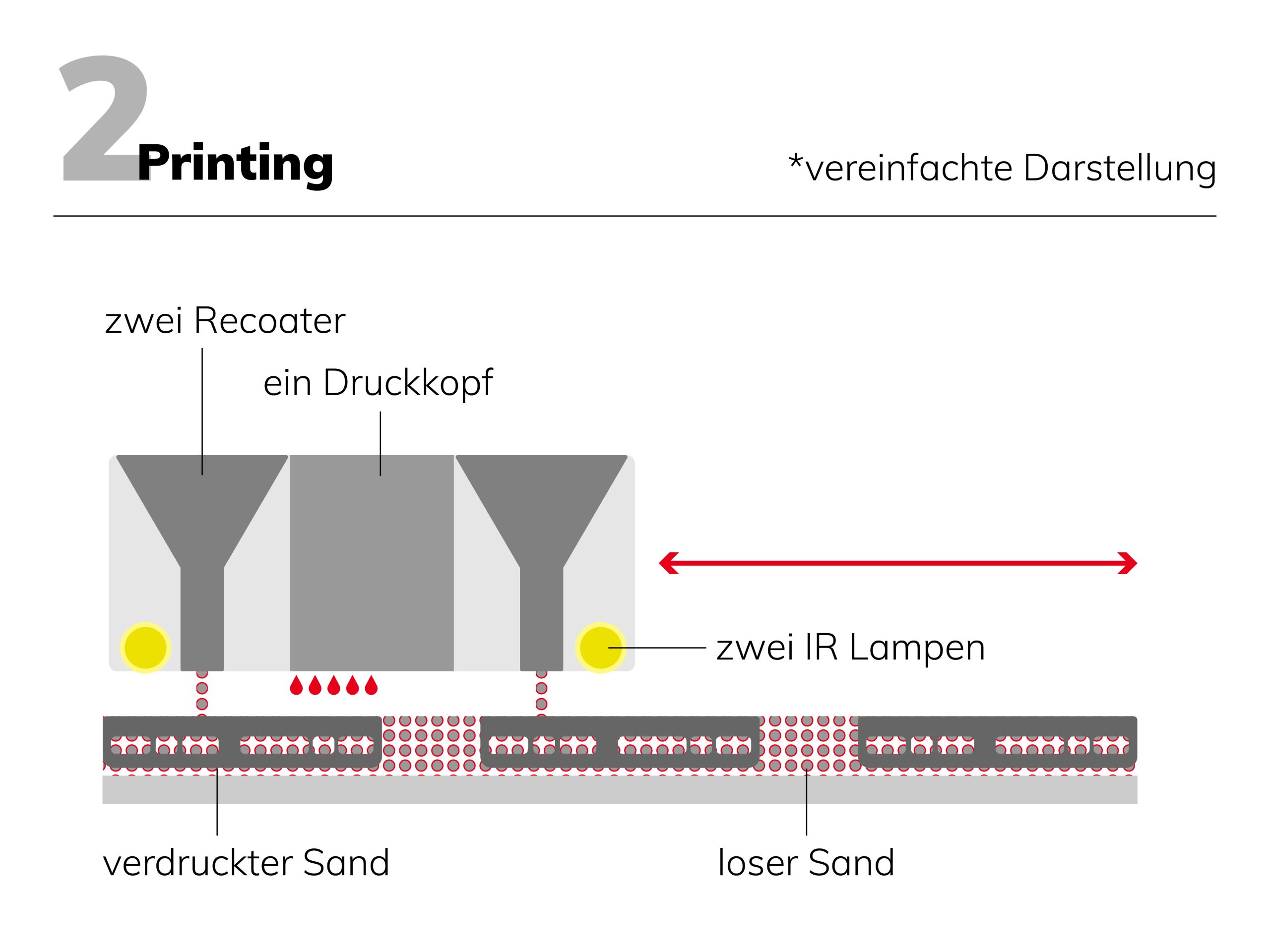
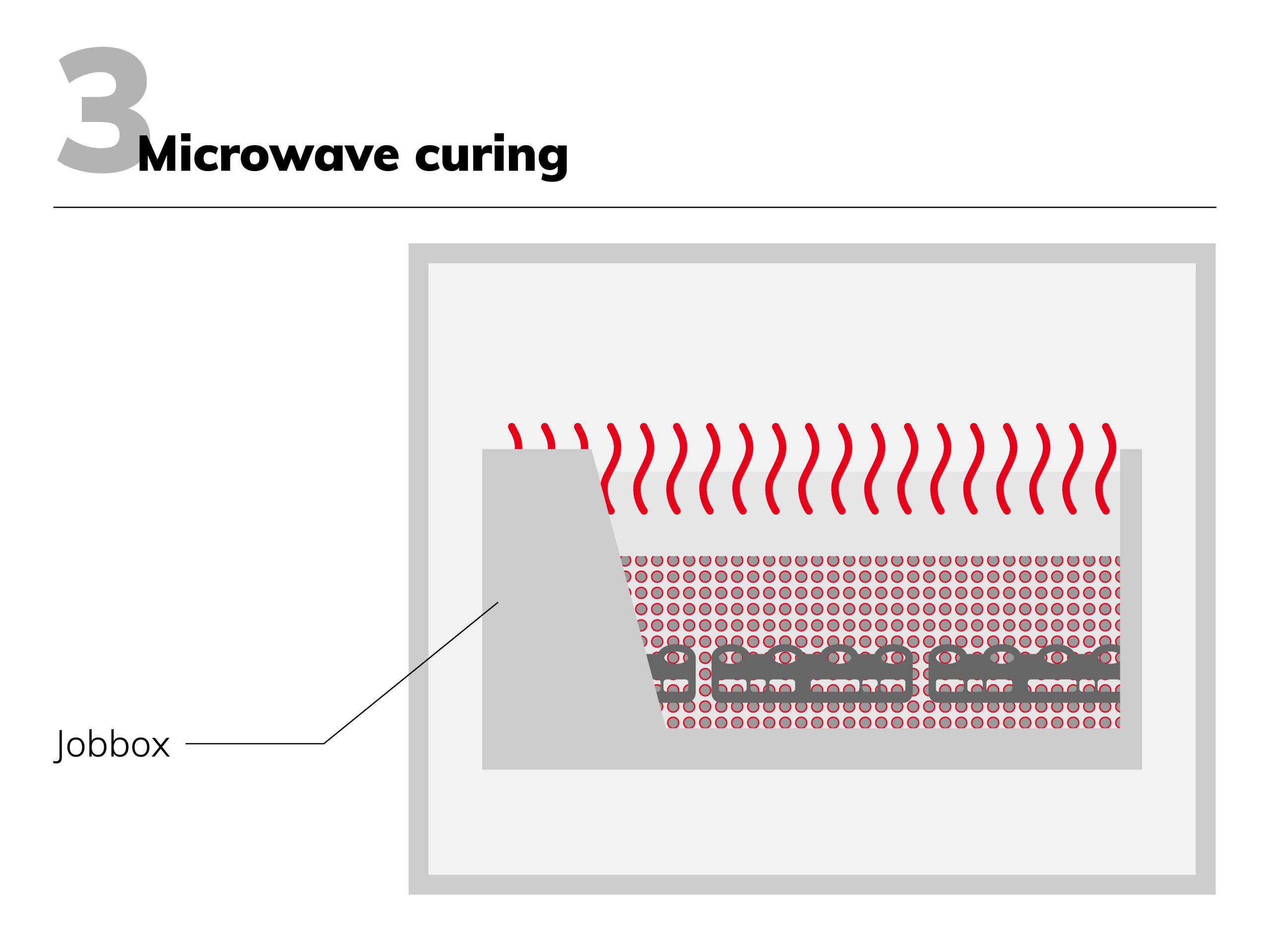
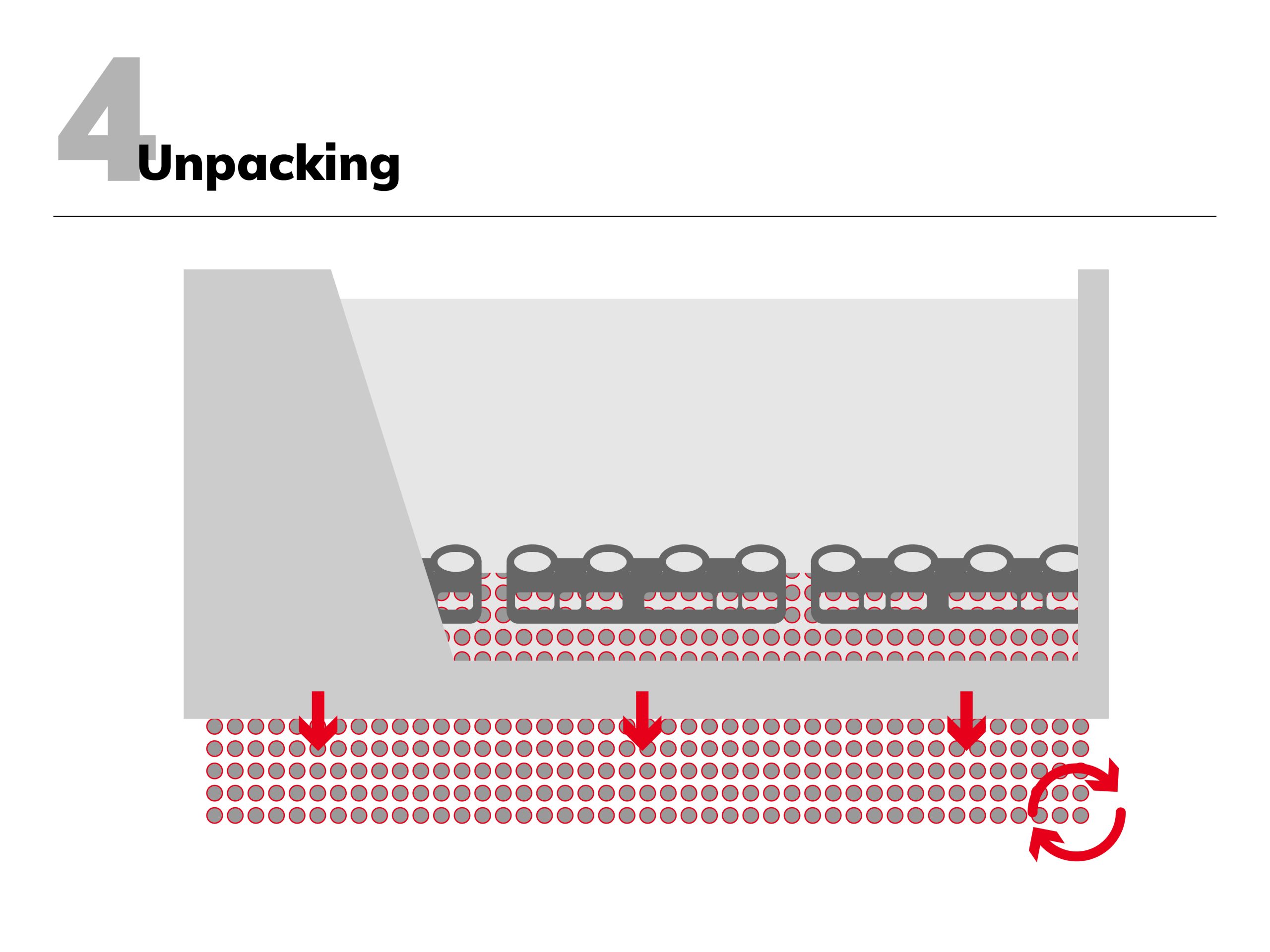
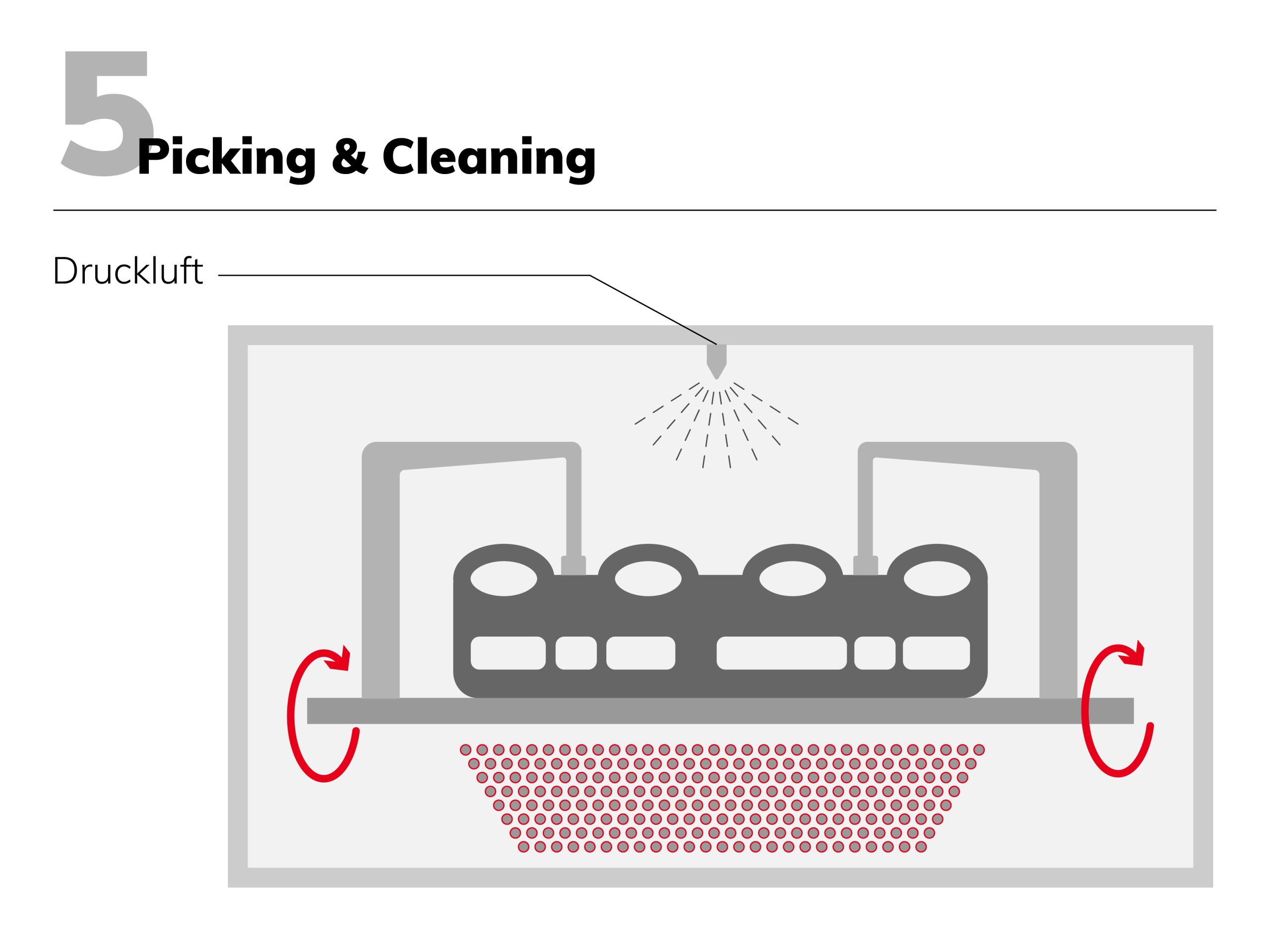
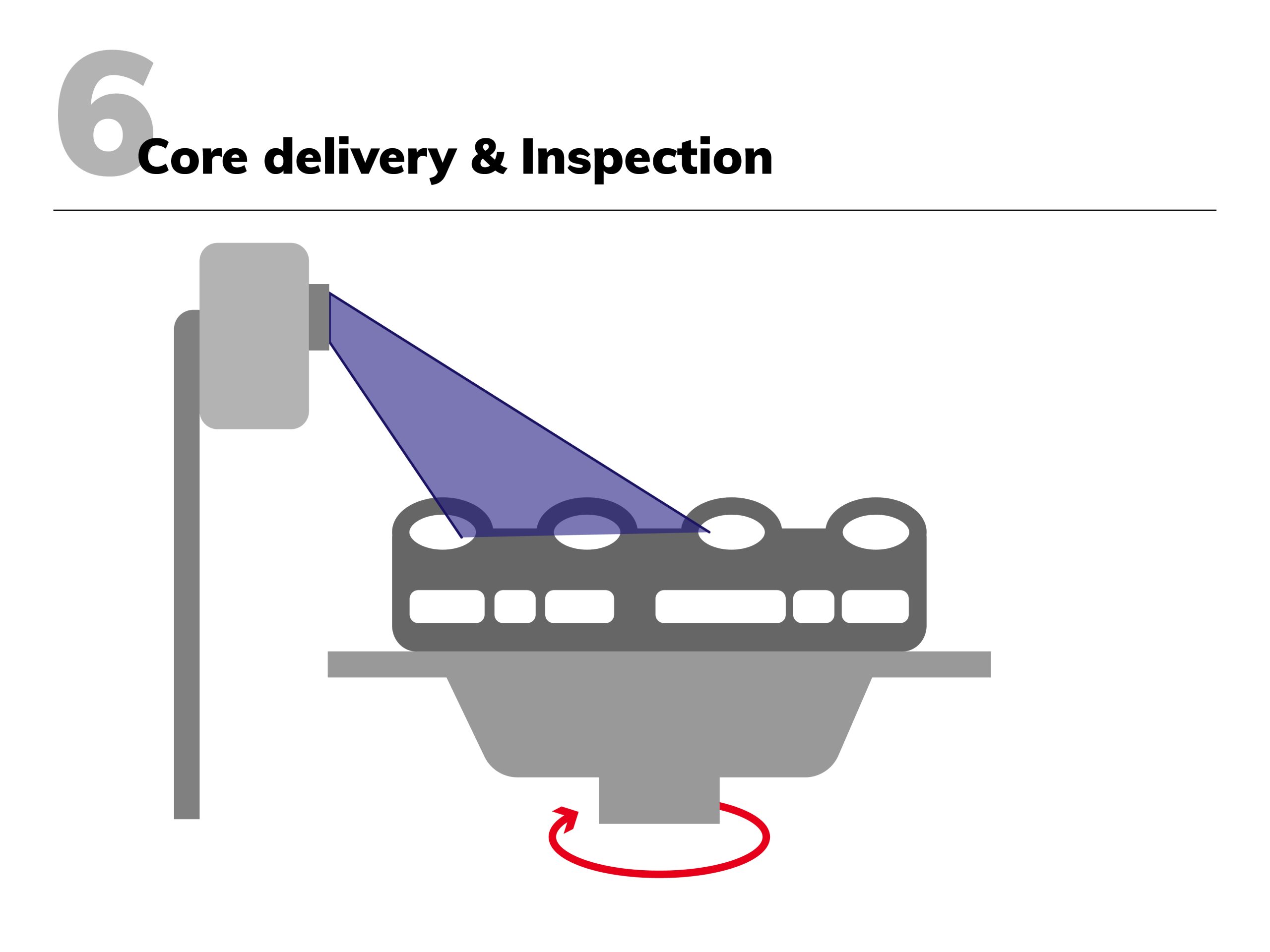
VX1300 X: Die Revolution der Casting Industrie
Um den Anforderungen an additive Serienfertigung gerecht zu werden, haben wir eigens für das ICP Projekt einen neuen 3D-Drucker entwickelt: die VX1300X. Ausgestattet mit redundanten Baugruppen, prädiktiver Wartung und einer einzigartigen Prozesseinheit setzt sie ein klares Statement um 3D-Druck in der Serie zu standardisieren.
Kontakt
Möchten Sie mehr erfahren? Dann fragen Sie uns. Wir helfen Ihnen gerne weiter.
3D-Drucklösungen
Sie möchten mehr über uns und den 3D-Druck erfahren? Hier geht’s zum gesamten Lösungsportfolio von voxeljet.