- Home
- Case Studies
- Gießerei
- Printed Casting – 3D-Druck für Gießereien
Printed Casting alsgünstige Alternativezum 3D-Metalldruck:So geht es!
Mit Binder Jetting 3D-Druck einen Schritt voraus: Automobilzulieferer GRATZ Engineering GmbH zeigt wie es geht. Mit der Integration von Sand-3D-Druck in ihre technischen Geschäftsfelder hat die Gratz Engineering GmbH ihrer Prototypenfertigung einen Schub in Richtung Wirtschaftlichkeit und Produktionsgeschwindigkeit gegeben.
Der Automobilzulieferer aus dem Nordosten Baden-Württembergs erkannte bereits in den Neunzigerjahren das enorme Potenzial des damals noch sehr jungen 3D-Drucks. GRATZ setzt seitdem auf den schnellen Metalldruck und den günstigen 3D-Druck von Sandgussformen.
Die GRATZ Engineering GmbH ist mit ihren 230 Mitarbeitern an mittlerweile sechs Standorten in Deutschland ein klassischer Mittelständler. Seit 1985 am Markt, setzten die Ingenieure bereits früh auf 3D-Druck für ihre Teilefertigung. Dabei kommen sowohl das Direct-Metal-Lasersintern (DMLS), also der direkte Metalldruck, als auch das 3D-Drucken von Sandformen oder Feingussmodellen für den Guss zum Einsatz.
Andreas Steinbronn, Abteilungsleiter Teilemanagement bei GRATZ erklärt, wieso ausgerechnet der 3D-Druck zu immensen Vorteilen bei Fertigungsgeschwindigkeit, Wirtschaftlichkeit und einer ganz neuen, disruptiven Herangehensweise im Design geführt hat. Das DMLS ist schnell, aber kostspielig; Hingegen ist der 3D-Sandformdruck mit anschließendem Gießen vergleichsweise günstig, aber für Rapid Prototyping teils nicht schnell genug. Doch was sind die Kriterien und Unterschiede zwischen Metall-3D-Druck und dem 3D-Druck unterstützten Guss von voxeljet?
Einflüsse des 3D-Drucks auf Geschäftsmodelle von Herstellern von Gussprodukten
Wir arbeiten vor allem mit zwei Verfahren: Dem Direct-Metal-Lasersintern und dem Guss mithilfe zugekaufter 3D-gedruckter Sandkerne und -formen und Feingussmodellen in der Prototypenfertigung. Bei gut fünf bis zehn Prozent aller unserer Aufträge kommt die additive Fertigung zum Einsatz. Obwohl der 3D-Druck bereits seit über vierzig Jahren in der Industrie Anwendungen findet, ist das Integrationsniveau im Vergleich zu anderen Verfahren wie dem klassischen Fräsen allerdings noch relativ gering. Bereits seit Mitte der Neunzigerjahre haben wir den 3D-Druck bei GRATZ schon mit im Boot. Unsere erste Einschätzung damals: Tolle Möglichkeiten tun sich hier auf, allein durch die Designfreiheit. Dadurch konnten wir den 3D-Druck schon sehr früh in unsere Entwicklungsprozesse einbinden. Das ist besonders interessant bei der technologischen und topologischen Optimierung von Bauteilen, hauptsächlich um Gewicht zu reduzieren. Heutzutage ist der 3D-Druck bei uns fast alltäglich geworden. Aber damals war das ein wirklich disruptiver Ansatz, den wir weiterhin auch noch heute verstärkt verfolgen.
Unsere erste Einschätzung damals: Tolle Möglichkeiten tun sich hier auf, allein durch die Designfreiheit. Dadurch konnten wir den 3D-Druck schon sehr früh in unsere Entwicklungsprozesse einbinden.
Andreas Steinbronn, AbteilungsleiterGRATZ Engineering GmbH
Aus dem Prototypenzentrum: Rapid Prototyping
Wir leisten immer noch ziemlich viel Aufklärungsarbeit, dass 3D-Druck viele Vorteile bietet. Besonders kundenseitig gibt es reichlich Informationsbedarf. Schnelligkeit ist das eine, dafür nehmen wir DMLS.
Wirtschaftlichkeit das andere, dann favorisieren wir den Sandgussformdruck von voxeljet. Grundsätzlich gilt aber: Wenn man die Bauteile aufgrund sehr komplexer Geometrien nicht fräsen kann, stellen wir sie via 3D-Druck her. Vor allem für Prototypen und Kleinserien. Neben Motorenkomponenten erstreckt sich die Anwendung auf alle weiteren Gebiete im Fahrzeug- aber auch Sondermaschinenbau.
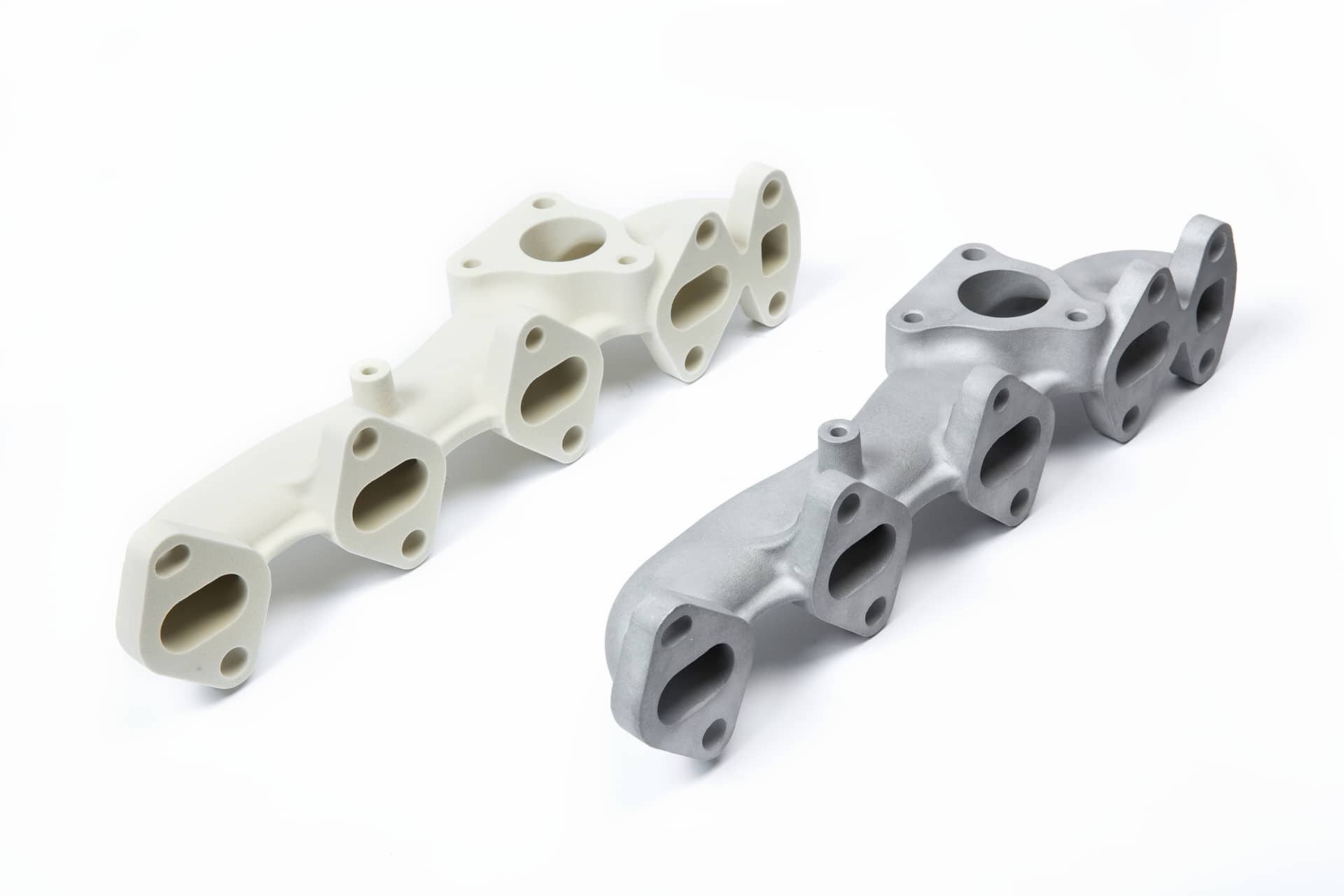
Schnelligkeit ist das eine, dafür nehmen wir DMLS. Wirtschaftlichkeit das andere, dann favorisieren wir den Sandgussformdruck von voxeljet. Grundsätzlich gilt aber: Wenn man die Bauteile aufgrund sehr komplexer Geometrien nicht fräsen kann, stellen wir sie via 3D-Druck her.
Andreas Steinbronn, AbteilungsleiterGRATZ Engineering GmbH
Unterschied zwischen gesinterten und gegossenen Teilen
Die Bauteilqualität und Materialhaltbarkeit von gesinterten Teilen ist mittlerweile so gut, dass bei entsprechender Nacharbeit und sogar bei hoher Fertigungsgeschwindigkeit 99 Prozent Bauteildichte realisierbar sind. Jedoch ist Lasersintern aufgrund der hohen Material- und Systempreise und noch relativ langsamen Baugeschwindigkeiten recht kostspielig.
Andreas Steinbronn fährt fort: „Metall-3D-Druck wie das Lasersintern ist immer zu teuer, wenn es nicht auf Geschwindigkeit ankommt. Wenn der Prototyp zwei bis drei Wochen Zeit hat, greifen wir generell lieber auf die Kombination des klassischen Gusses mit 3D-gedruckten Sandformen oder Feingussmodellen aus PMMA zurück. Das spart enorm Kosten und die erhöhte Lebensdauer und Stabilität der Bauteile ist natürlich auch von Vorteil. Das Praktische dabei sind die großen Bauräume und hohen Druckraten. Denn in den Bauräumen der Binder Jetting Drucksysteme können wir bei einem 3D-Druckvorgang direkt mehrere Varianten unserer Prototypen, wie beispielsweise Turbolader, parallel und übereinander geschachtelt herstellen, nicht wie im DMLS nur in einer Ebene. Wir nutzen das Volumen des Bauraums, auch Jobbox genannt, bestmöglich aus. So können wir die anschließenden Tests parallelisieren, was zusätzlich Zeit spart. Das kostet zwar, im Vergleich zum Lasersintern, immer noch etwas mehr Zeit, aber dafür können wir eben direkt unterschiedliche Varianten des Bauteils gleichzeitig testen, um ein finales Design schnellstmöglich zu definieren und für die Produktion freizugeben. Zudem haben wir eine deutlich größere Materialvielfalt beim Guss. Wir können eigentlich mit beliebigen Legierungen arbeiten. Beim Sintern hingegen sind wir deutlich eingeschränkter.“ Im Anschluss zur additiven Fertigung muss bei beiden Verfahren meist eine mechanische Nachbearbeitung erfolgen.
Wir haben beim Guss eine deutlich größere Materialvielfalt. Wir können eigentlich mit beliebigen Legierungen arbeiten. Beim Sintern hingegen sind wir deutlich eingeschränkter.
Andreas Steinbronn, AbteilungsleiterGRATZ Engineering GmbH
Wann DMLS und wann 3D-Druck und Guss?
Im Moment konkurriert das Direct-Metal-Lasersintern mit Gießereien in einem vergleichsweise kleinen Segment. Die Bauräume der DMLS-Anlagen eignen sich in erster Linie für kleinere Bauteile, die extrem schnell hergestellt werden sollen. Allerdings ist der direkte 3D-Metalldruck eben auch sehr teuer.
Für das DMLS ist nach additiver Fertigung ein paralleles heißisostatisches Pressen (HIP) notwendig, um eine ausreichend gute Bauteildichte und Festigkeit zu erzielen. „Unterm Strich liegen die Durchschnittspreise für 3D-gedruckte Metallbauteile daher bei rund 300 Euro pro Kilogramm bei Aluminium, 400 Euro bei Edelstahl und bis zu 1.300 Euro pro Kilogramm für Sonderlegierungen. Im direkten Vergleich liegt der reine Metallgusspreis beim 3D-Sanddruck bei zirka 6,50 bis 32 Euro pro Kilo der Liter gedrucktes Material bei zirka neun Euro“, sagt GRATZ-Abteilungsleiter Steinbronn.
„Mit etwas mehr Zeit können wir Bauteile mit komplexen Geometrien in kleinen Serien von bis zu einhundert Stück oder in Losgröße eins auch durch Gießen wirtschaftlich herstellen“, fährt Steinbronn fort. „Voraussetzung ist, dass wir die Formen, Kerne und Modelle schnell und kostengünstig herstellen können, ohne teure Spezialwerkzeuge. Genau hier kommt der industrielle 3D-Druck von voxeljet ins Spiel.“
Das Rapid Casting genannte Verfahren druckt die für den Guss benötigten Formen und Kerne komplett werkzeuglos in gießereiüblichen Materialien. voxeljets VX4000 ist derzeit der weltweit größte 3D-Drucker für Sandformen mit einem Bauraum von 4.000 x 2.000 x 1.000 Millimetern.
Das System ermöglicht die schnelle und automatisierte Herstellung der Gussformen mithilfe des leistungsstarken Binder-Jetting-Verfahrens. Einen weiteren Ansatz bietet das PMMA Materialset von voxeljet. Mittels dieser Kunststoffe lassen sich Modelle werkzeuglos drucken, die anschließend im Feingussverfahren wie konventionelle Wachslinge verarbeitet werden können.
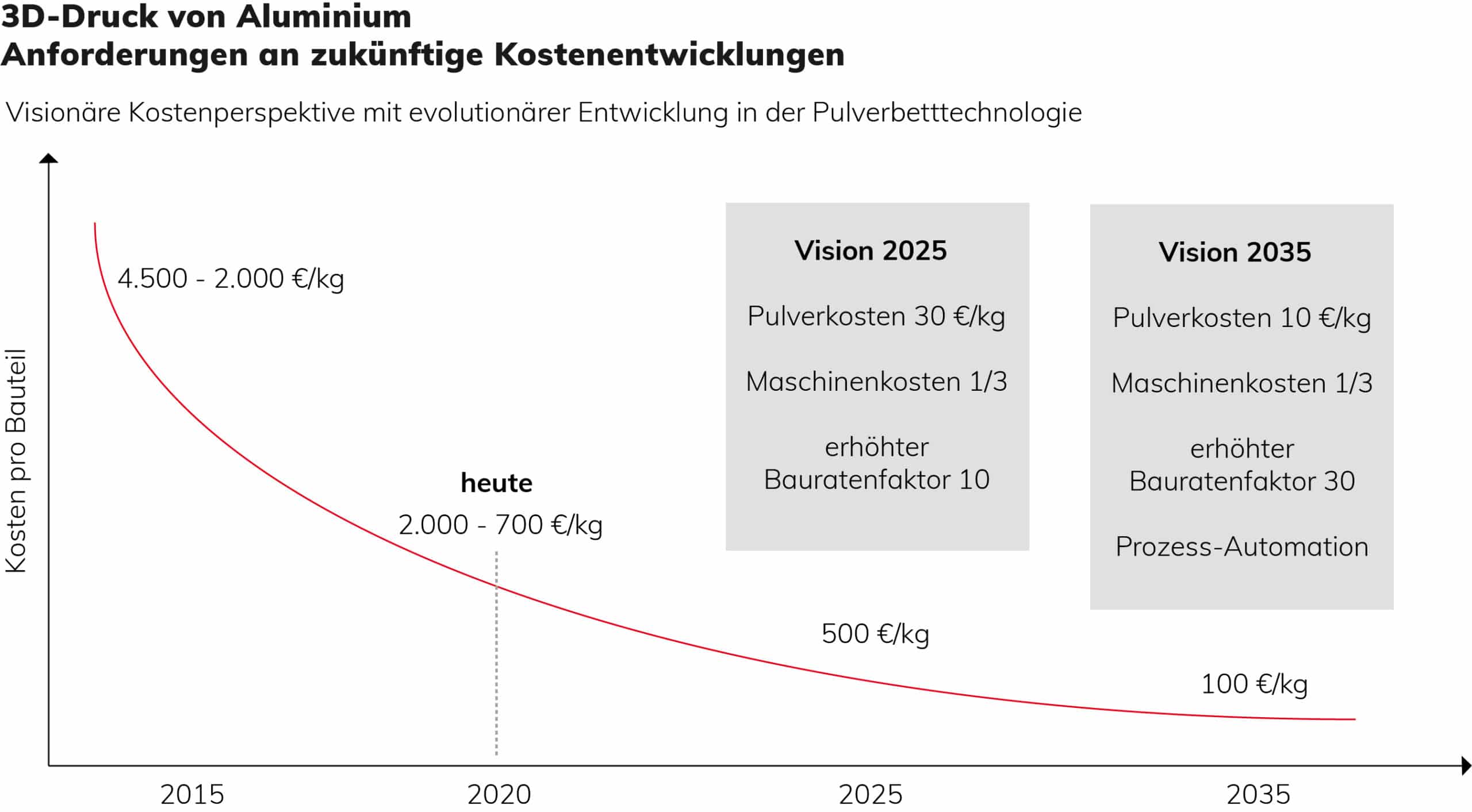
DMLS versus 3D-Druck und Guss: Wo fängt die Reise an und wo geht sie hin?
Die GRATZ Engineering GmbH ist nur eines von vielen Beispielen, die den 3D-Druck in verschiedenen Formen fest in ihr Geschäftsmodell integriert hat. Die Technologie heute nicht mehr zu nutzen, kommt für den Engineeringexperten GRATZ nicht mehr in Frage. Denn die Vorteile hinsichtlich Lieferzeiten, Wirtschaftlichkeit und Leistungssteigerung durch geometrische Freiheit sind einfach zu groß.
„Das Gute ist, dass man als mittelständisches Unternehmen nicht darauf angewiesen ist, gleich in ein eigenes Drucksystem zu investieren. Um erste Erfahrungen zu sammeln wie sich die gedruckten Bauteile und Formen verhalten und einsetzten lassen lohnt es sich, auf die On-Demand-Dienstleistung zu setzen. Das ist ein bequemer Einstieg mit mehr oder weniger den gleichen positiven Effekten wie die Anschaffung eines eigenen 3D-Drucksystemes“, erklärt Steinbronn. Heute fertigt die GRATZ Engineering GmbH allerlei Motorenkomponenten additiv: von Halterungen über Abgaskrümmer bis hin zu Zylinderköpfen. Besonders im Hinblick auf eine erhöhte Effizienz und Nachhaltigkeit in der Automobilindustrie empfiehlt GRATZ den Einsatz der Technologie. „Aufgrund der großen geometrischen Freiheit ermöglicht es der 3D-Druck uns Ingenieuren, völlig neue Blickwinkel im Design und der Konstruktion von Komponenten einzunehmen und auch bewährte Bauteile neu zu evaluieren. Durch 3D-Druck können wir uns von der Idee den Design for Manufacturing, also dem Design für eine wirtschaftliche Produktion mit klassischen Fertigungsverfahren lösen. Wir können endlich eher in die Richtung Design for Functionality, also dem Optimieren von Bauteilen hinsichtlich ihrer Funktionalität und Effizienz, denken. Das lässt sowohl das Herz des Ingenieurs als auch das des Unternehmers höherschlagen. Denn selbst die komplexesten Designs lassen sich mittels 3D-Druck wirtschaftlich herstellen. Daher sehen wir in der Technologie ein enormes Zukunftspotenzial“, schließt Steinbronn ab.
Der Binder-Jetting Prozess im Rapid Casting: So geht es!
Das 3D-Drucksystem breitet auf der Bauplattform eine 300 Mikrometer dünne Sandschicht aus. Anschließend verklebt der Druckkopf mit einem Bindemittel die Sandkörner überall dort, wo die Sandgussform entstehen soll. Die Bauplattform senkt sich um eine Schichtstärke ab und der Prozess beginnt erneut, bis die Form fertiggestellt ist. Der überschüssige Sand wird anschließend entfernt, nun ist die Form bereit für den Guss. Die gedruckten Formen und Kerne können zudem jederzeit mit einfachen, konventionell hergestellten Gussformen kombiniert werden.
Anders als beim Sanddruckverfahren, bei dem eine Negativform des gewünschten Bauteiles gedruckt wird, wird beim PMMA-Materialset für den Feinguss ein Positivmodell – auch Urmodell genannt – aus Kunststoffpulver gedruckt. Dieses Modell wird in einer Feingießerei mit einer Keramik ummantelt und anschließend ausgebrannt. Übrig bleibt eine hohle Keramikform in die gegossen werden kann. Der Vorteil liegt dabei in der Möglichkeit, deutlich präzisere Strukturen und Oberflächen gießen zu können.
Weitere Case Studies
PMMA 3D-Druck erobert Nordamerika
Express Prototyping gehört zu den führenden Experten für den 3D-Druck von Feingussmodellen in Nordamerika. Erfahren Sie vom Geschäftsführer Thomas Müller, wie er das Unternehmen gegründet hat und wie er die Zukunft sieht.
Boro Foundry – Superheater Header
Aus der Kombination Sand-3D-Druck konnte die britische Gießerei Boro Foundry ein makelloses Ersatzteil für eine Dampflok herstellen.
Mit 3D-Druck zum Optimierten Elektromotor
Aiona Cast hat ein Patent angemeldet mit dem sich Elektromotoren deutlich optimieren lassen. Einen Prototyp fertigte das Unternehmen mit 3D-Druck an.
Die schnellste Gießerei Skandinaviens
Mit einer neuen VX2000, einem 3D-Sanddrucker für Metallguss stellt Hetitec fertige Gussteile in wenigen Tagen her.
Printed Castings für den Feinguss
Ob Luft- und Raumfahrt, Automobilbau oder Design - die preisgekrönte, amerikanische Feingießerei Aristo Cast setzt beim Feinguss auf 3D-gedruckte Modelle. Erfahren Sie hier warum.
Printed Casting Gehäuse für E-Motorrad
Durch den Einsatz innovativer Technologien wie dem 3D-Druck könnte der Prototyp schon bald in Serie gehen.
Printed Castings: 3D-Druck für den Leichtbau und die Elektromobilität
Vor der Serienreife zum perfekten Prototypen. Die britische Gießerei BCP setzt nicht nur bei Elektromotorgehäusen auf 3D gedruckte Formen und Kerne.
Kontakt
Möchten Sie mehr erfahren? Dann fragen Sie uns. Wir helfen Ihnen gerne weiter.
Industrielle 3D-Drucksysteme
Unser Portfolio an industriellen 3D-Druckern reicht vom kompakten System für die Forschung bis zur additiven Serienfertigung.